Friction stir welding for heat sinks with high-density connections
Cooling manufacturing process for dimensionally stable heat sinks with high cooling capacity
Instead, the metal is made malleable by frictional heat and stirred and compacted by a rotating tool. This results in a consistent, media- and pressure-tight weld seam of high, reproducible quality. Another advantage of friction stir welding is the robustness of the process against material defects such as pores or hot cracks. This makes it particularly attractive for the production of aluminium heat sinks as liquid heat sinks, as their joints require high thermal conductivity, tightness and reliability.
Advantages of the friction welding manufacturing process
- Uniform joint structure with excellent mechanical and heat transfer properties
- Homogeneous, hard-wearing welded joints that are completely tight and non-porous
- Mixed material ensures excellent and uniform thermal conductivity
- Friction stir welding makes it possible to produce aluminium heat sinks with high fins and therefore very large designs
- Low temperatures during the process prevent structural changes
- No additives or shielding gases required during production
- Various surface finishes possible
(anodising, chromating, painting, powder coating, etc.)
Friction welding in combination with various techniques
Friction Stir Welding FSW+ scalable width
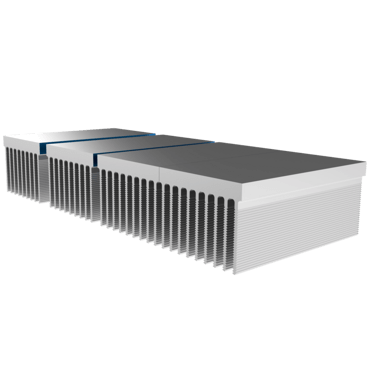
Friction Stir Welding FSW+ heat pipes
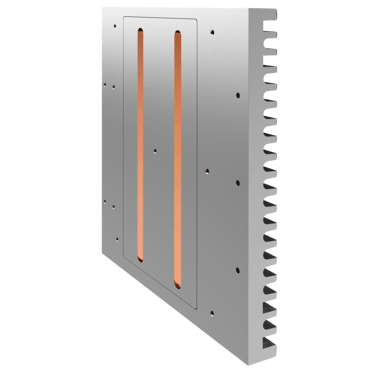
Friction Stir Welding FSW+ fluid channels
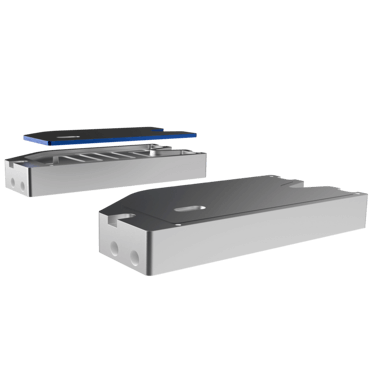
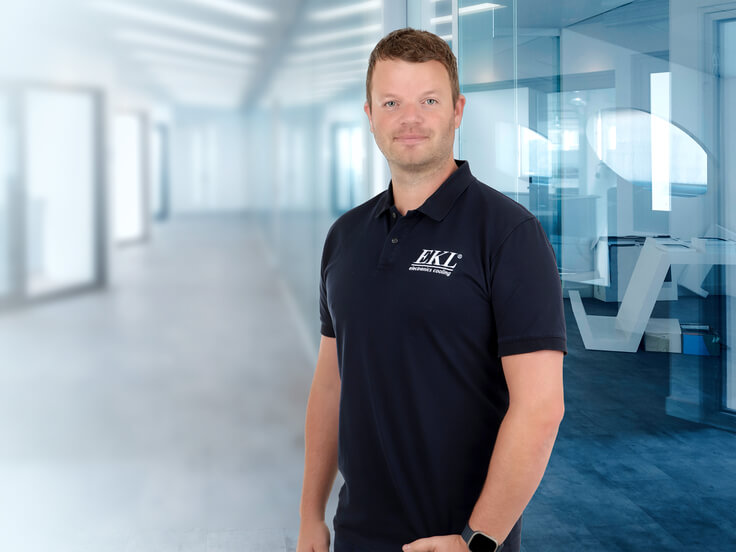
Thomas Würzer
Sales Department
+49 (0)7561 9837-44
t.wuerzer@ekl-ag.de
Make an appointment Enquiries by e-mail
Special areas of application for friction welding
- Aluminium heat sinks with large widths and tall fin heights
- Liquid heat sinks in which the top and bottom plates are connected by friction stir welding
- Power converter coolers for the railway industry, in particular IGBT coolers for electric locomotives and railcars
- Thin sheet coolers for cooling batteries and battery cooling plates for electric lorries
- Water-cooled die-cast aluminium parts
- Aluminium/copper, aluminium/brass and copper/brass mixed connections
Added value and extras
Welcome to EKL!
CNC machining
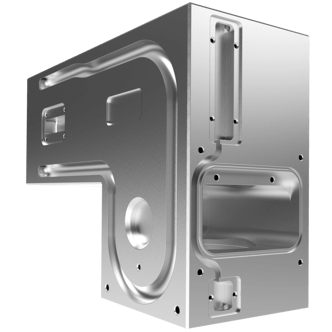
Hermle C 400 (5-axis) 850 x 700 x 500 mm | Mikron VCE1000pro (3-axis) 1000 x 560 x 600 mm | Kondia B1050 (3-axis): 1000 x 500 x 600 mm
Surface finishing
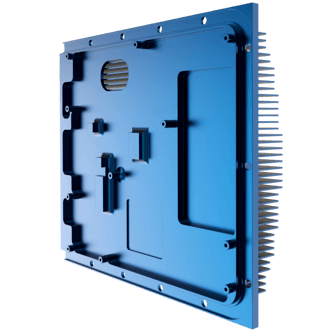
Attachments & accessories
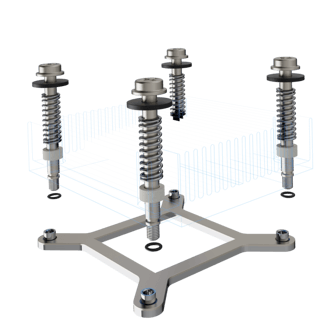
Secure packaging for transport
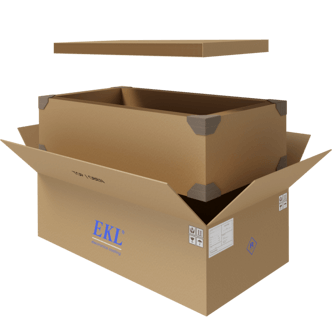
FSW heat sinks in typical areas of application
The EKL project stages for your cooling solutionChoose your point of entry!
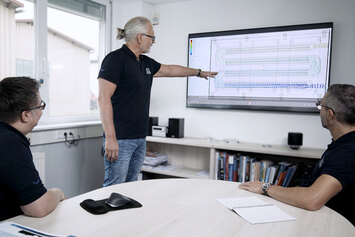
Concept
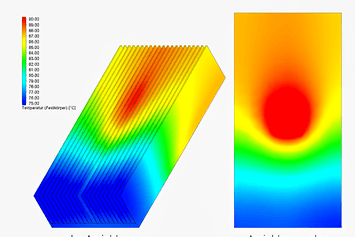
Feasibility / simulation

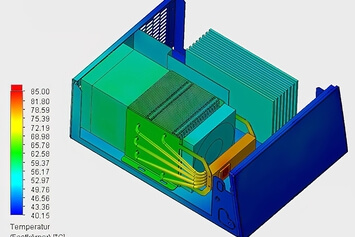
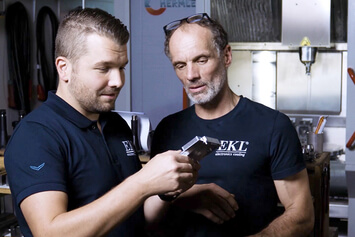
Prototype construction
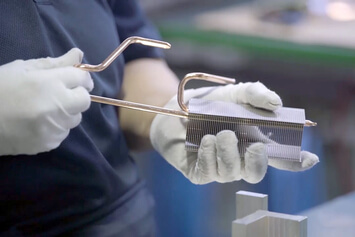
small to large
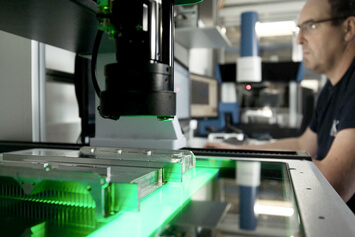
Incoming goods inspection
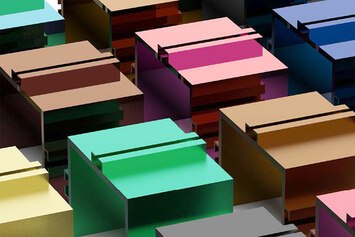
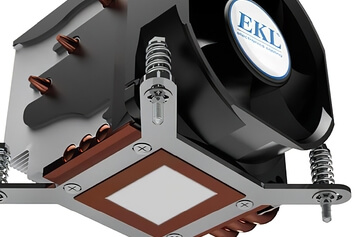
Pre-assembly
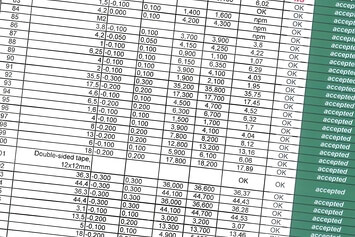
Test plans
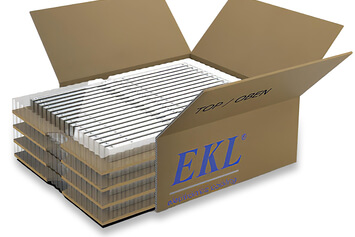
Packaging production
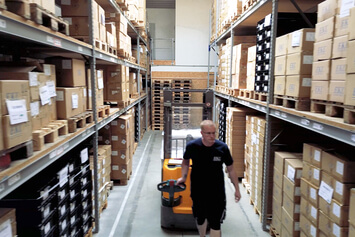
& Logistics
Direct comparison of friction stir welding manufacturing processes
Extruded heat sinks | Cold forged heat sinks | Soldered heat sinks | Bonded cooling fins | Pressed cooling fins | Friction stir welding | Heatpipes | Vapour Chamber | Crimped heat sinks | Skived Fins | Die casting | Laserwelding | Vacuum brazing | |
---|---|---|---|---|---|---|---|---|---|---|---|---|---|
Thermal conductivity | |||||||||||||
Heat dissipation over long distances | |||||||||||||
Design freedom and flexibility in shape and size | |||||||||||||
Low tool costs / initial investment | |||||||||||||
Favourable unit prices | |||||||||||||
Low set-up costs | |||||||||||||
Economic efficiency for small series | |||||||||||||
Economic efficiency for large series | |||||||||||||
Can be combined with other technologies | |||||||||||||
Surface finishing / resistance | |||||||||||||
Heat transfer | |||||||||||||
Standard products | |||||||||||||
Material density | n.a. | n.a. | n.a. | n.a. | n.a. | n.a. | |||||||
Space-saving, large surface area in a small space | |||||||||||||
Weight-saving | |||||||||||||
Position dependence / gravity dependence | |||||||||||||
Machinability | |||||||||||||
Mechanical stability | |||||||||||||
Low wear and tear | |||||||||||||
Homogeneity (material, no additional materials) | |||||||||||||
Suitability for large coolers | |||||||||||||
Suitability for small coolers |
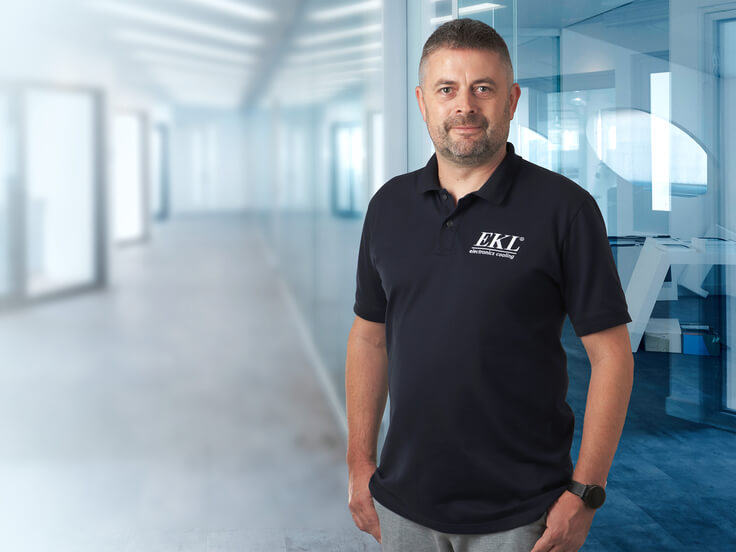
Frank Sichler
Sales Manager
+49 (0)7561 9837-47
f.sichler@ekl-ag.de
Make an appointment Enquiries by e-mail