Aluminium die-cast heat sinks and housings in complex geometries
Ideal for filigree as well as voluminous heat sinks in large quantities
Advantages of aluminium die-casting in heat sink production
- Complex geometries and fine structures possible
- Efficient heat dissipation via the aluminium material
- Cost efficiency with high quantities
- Lightweight zinc or aluminium die-cast parts with high temperature resistance
- Reliable cooling function of the dimensionally stable, rigid zinc/aluminium heat sinks
- Only minimal CNC post-processing required
- Various surface finishes possible
(anodising, chromating, painting, powder coating, etc.)
Increased performance of die-cast aluminium heat sinks through a combination of different techniques
Aluminium die-cast heat sinks+ surface finishing
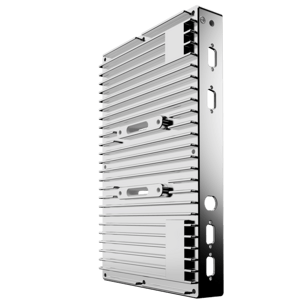
Die-cast aluminium heat sink+ fan
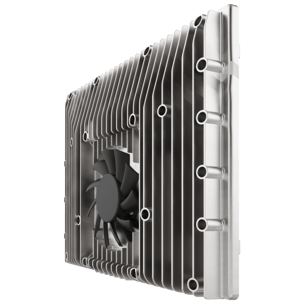
Aluminium die-cast heat sink+ heatpipe
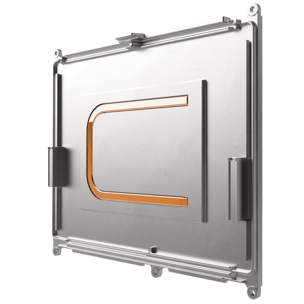
Die-cast aluminium heat sink+ vapour chamber
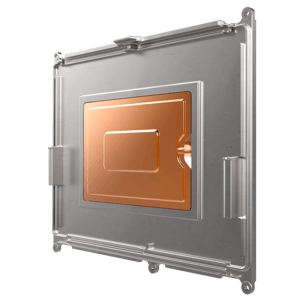
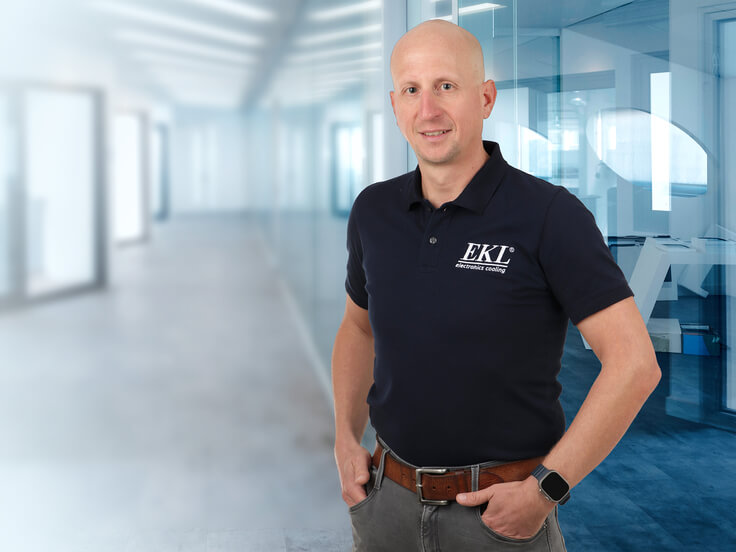
Danny Weimer
Sales Department
+49 (0)7561 9837-28
d.weimer@ekl-ag.de
Make an appointment Enquiries by e-mail
Aluminium die-cast housing as heat sink for POI/HMI displays and more
The integration of a mounting bracket into the die-cast aluminium housing is also easy to implement. This means that a die-cast aluminium heat sink is not only used to cool electronic components, but also as a robust motor housing or a stylish rear panel for a panel application such as POI / HMI displays, for example.
Cost-optimised and scalable in terms of mould and production volume
Added value and extras
Welcome to EKL!
CNC machining
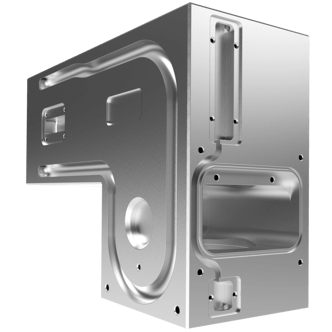
Hermle C 400 (5-axis) 850 x 700 x 500 mm | Mikron VCE1000pro (3-axis) 1000 x 560 x 600 mm | Kondia B1050 (3-axis): 1000 x 500 x 600 mm
Surface finishing
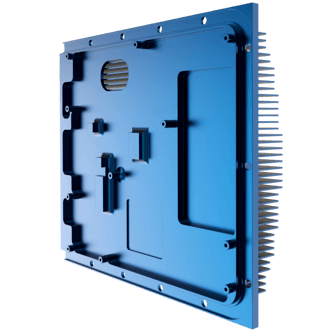
Attachments & accessories
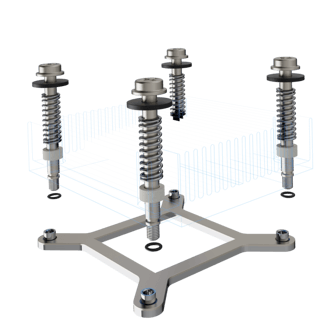
Secure packaging for transport
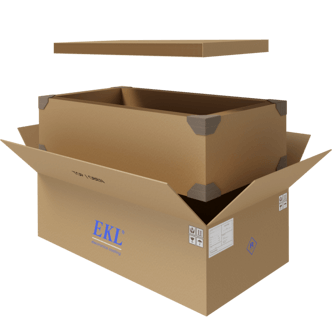
EKL: Your aluminium die-cast manufacturer for heat sinks in electronic systems
The EKL project stages for your cooling solutionChoose your point of entry!
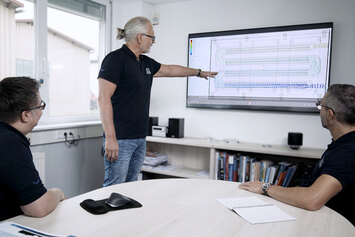
Concept
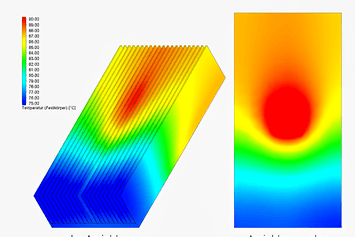
Feasibility / simulation

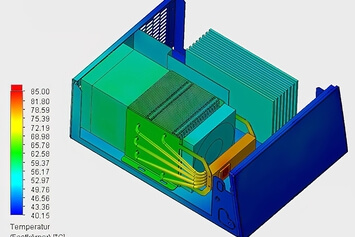
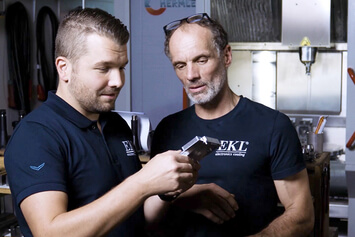
Prototype construction
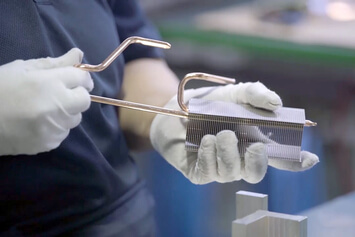
small to large
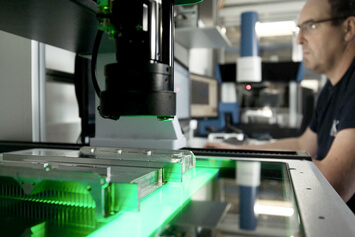
Incoming goods inspection
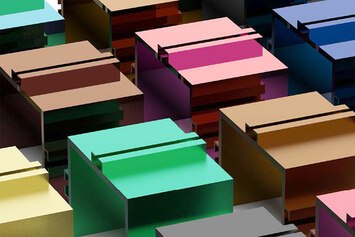
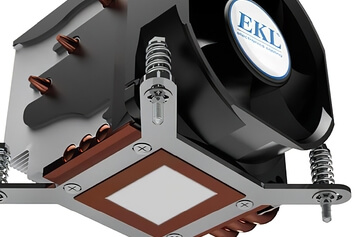
Pre-assembly
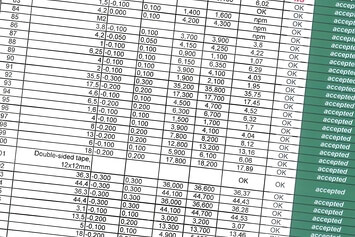
Test plans
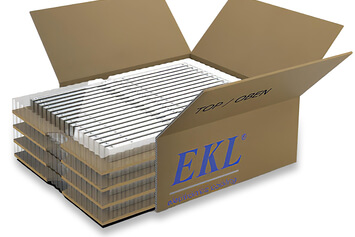
Packaging production
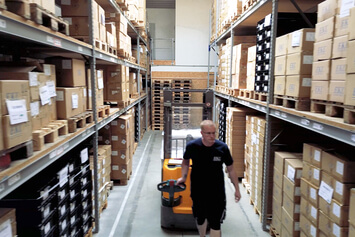
& Logistics
Direct comparison of the cast manufacturing processes
Extruded heat sinks | Cold forged heat sinks | Soldered heat sinks | Bonded cooling fins | Pressed cooling fins | Friction stir welding | Heatpipes | Vapour Chamber | Crimped heat sinks | Skived Fins | Die casting | Laserwelding | Vacuum brazing | |
---|---|---|---|---|---|---|---|---|---|---|---|---|---|
Thermal conductivity | |||||||||||||
Heat dissipation over long distances | |||||||||||||
Design freedom and flexibility in shape and size | |||||||||||||
Low tool costs / initial investment | |||||||||||||
Favourable unit prices | |||||||||||||
Low set-up costs | |||||||||||||
Economic efficiency for small series | |||||||||||||
Economic efficiency for large series | |||||||||||||
Can be combined with other technologies | |||||||||||||
Surface finishing / resistance | |||||||||||||
Heat transfer | |||||||||||||
Standard products | |||||||||||||
Material density | n.a. | n.a. | n.a. | n.a. | n.a. | n.a. | |||||||
Space-saving, large surface area in a small space | |||||||||||||
Weight-saving | |||||||||||||
Position dependence / gravity dependence | |||||||||||||
Machinability | |||||||||||||
Mechanical stability | |||||||||||||
Low wear and tear | |||||||||||||
Homogeneity (material, no additional materials) | |||||||||||||
Suitability for large coolers | |||||||||||||
Suitability for small coolers |
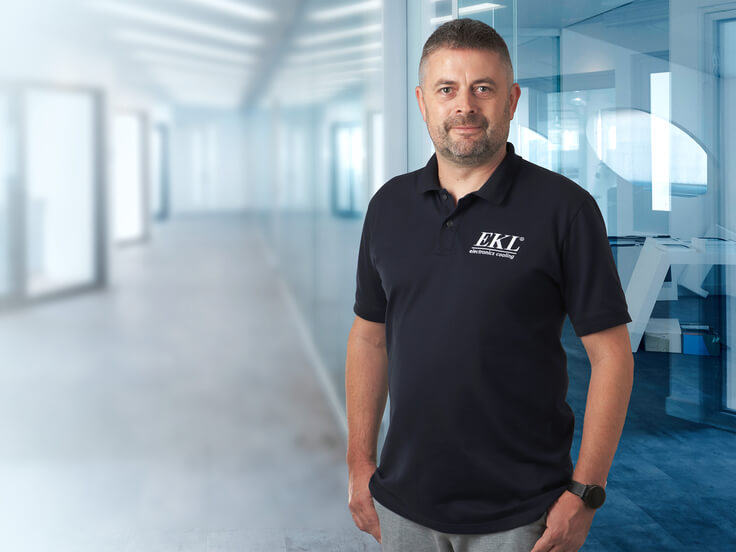
Frank Sichler
Sales Manager
+49 (0)7561 9837-47
f.sichler@ekl-ag.de
Make an appointment Enquiries by e-mail