Cold forging pin fin heat sinks using the cold extrusion process
Pin fin heat sinks pressed from aluminium or copper in a single work process
Advantages of cold forging
- Copper heat sink and aluminium heat sink "in one piece"
- High-purity aluminium or copper with very good thermal conductivity
- High material compaction further improves thermal conductivity
- Tight dimensional tolerances achievable
- Large surface area possible thanks to round pins
- Increased strength and robustness
- Standard sizes and shapes available
- Various surface finishes possible
(anodising, chromating, painting, powder coating, etc.)
Increased performance of pin fin heat sinks by combining different techniques
Pin Fin heat sink+ fan
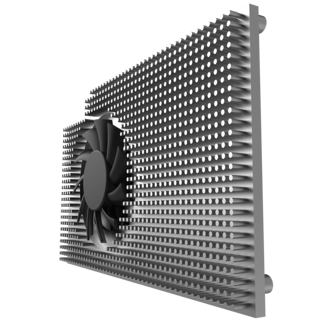
Pin Fin heat sink+ plastic air duct
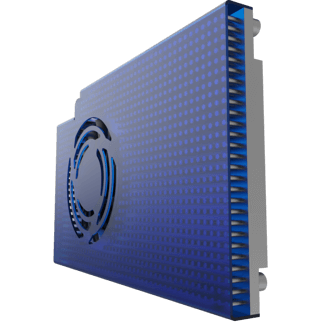
Pin Fin heat sink+ heatpipes
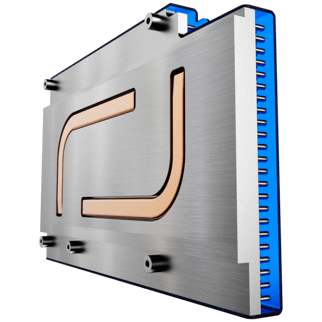
Pin Fin heat sink+ vapour chamber
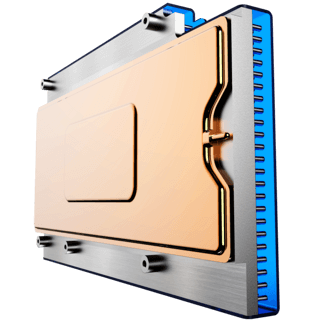
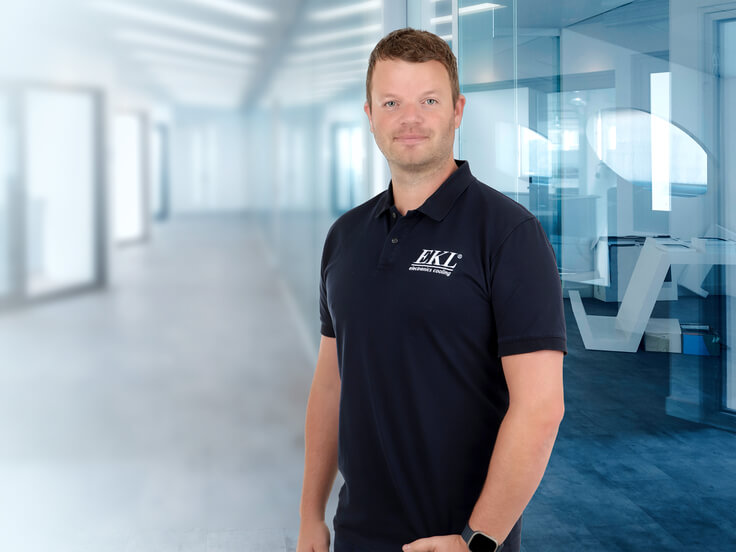
Thomas Würzer
Sales Department
+49 (0)7561 9837-44
t.wuerzer@ekl-ag.de
Make an appointment Enquiries by e-mail
Pin Fin Cooling for high heat dissipation and cooling performance
Thanks to their design, pin heat sinks enable rapid heat spreading and effective heat dissipation, even in compact spaces. The high material density and high thermal conductivity of the pure aluminium alloys or copper alloys help to ensure that the heat is conducted quickly from the base plate to the tips of the pins. This is particularly advantageous in conjunction with forced convection, i.e. when a fan supports heat dissipation.
Added value and extras
Welcome to EKL!
CNC machining
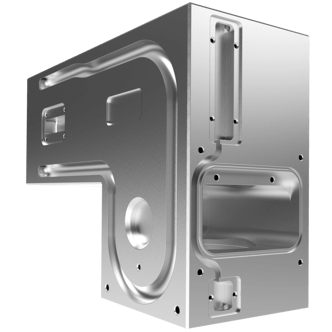
Hermle C 400 (5-axis) 850 x 700 x 500 mm | Mikron VCE1000pro (3-axis) 1000 x 560 x 600 mm | Kondia B1050 (3-axis): 1000 x 500 x 600 mm
Surface finishing
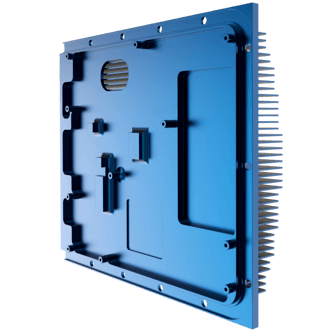
Attachments & accessories
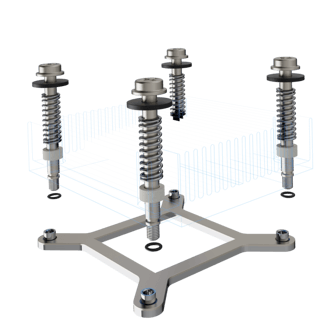
Secure packaging for transport
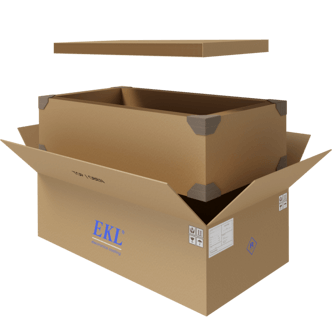
Cold forged heat sinks in typical application areas
The EKL project stages for your cooling solutionChoose your point of entry!
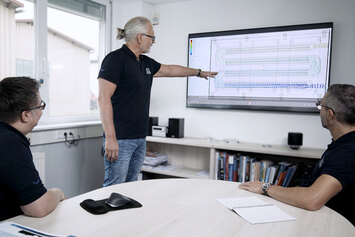
Concept
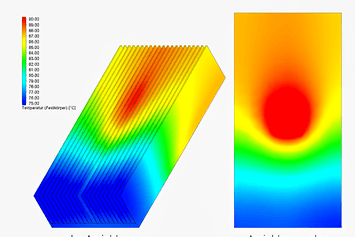
Feasibility / simulation

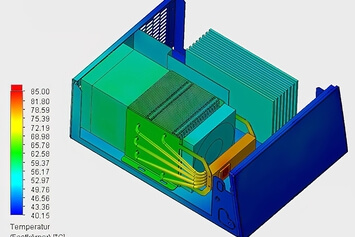
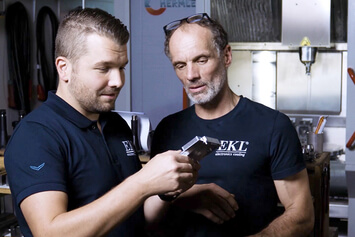
Prototype construction
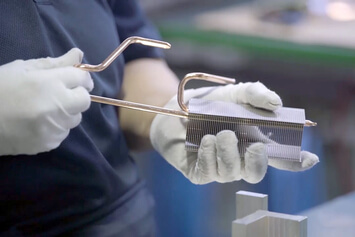
small to large
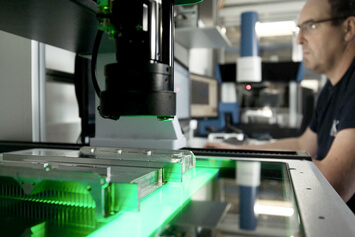
Incoming goods inspection
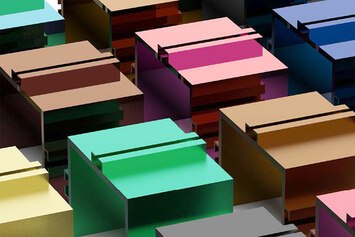
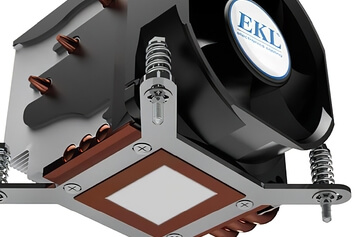
Pre-assembly
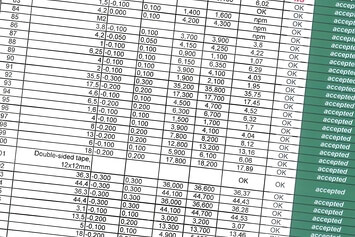
Test plans
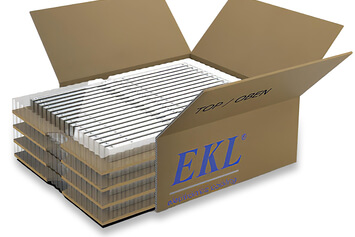
Packaging production
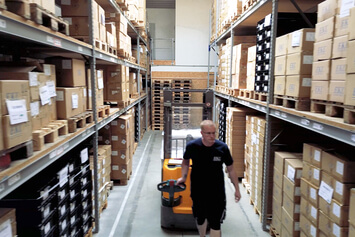
& Logistics
Direct comparison of cold forging manufacturing processes
Extruded heat sinks | Cold forged heat sinks | Soldered heat sinks | Bonded cooling fins | Pressed cooling fins | Friction stir welding | Heatpipes | Vapour Chamber | Crimped heat sinks | Skived Fins | Die casting | Laserwelding | Vacuum brazing | |
---|---|---|---|---|---|---|---|---|---|---|---|---|---|
Thermal conductivity | |||||||||||||
Heat dissipation over long distances | |||||||||||||
Design freedom and flexibility in shape and size | |||||||||||||
Low tool costs / initial investment | |||||||||||||
Favourable unit prices | |||||||||||||
Low set-up costs | |||||||||||||
Economic efficiency for small series | |||||||||||||
Economic efficiency for large series | |||||||||||||
Can be combined with other technologies | |||||||||||||
Surface finishing / resistance | |||||||||||||
Heat transfer | |||||||||||||
Standard products | |||||||||||||
Material density | n.a. | n.a. | n.a. | n.a. | n.a. | n.a. | |||||||
Space-saving, large surface area in a small space | |||||||||||||
Weight-saving | |||||||||||||
Position dependence / gravity dependence | |||||||||||||
Machinability | |||||||||||||
Mechanical stability | |||||||||||||
Low wear and tear | |||||||||||||
Homogeneity (material, no additional materials) | |||||||||||||
Suitability for large coolers | |||||||||||||
Suitability for small coolers |
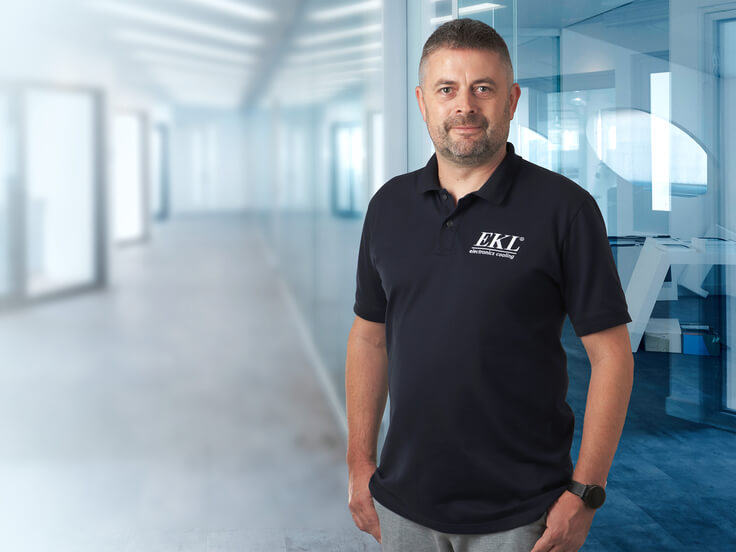
Frank Sichler
Sales Manager
+49 (0)7561 9837-47
f.sichler@ekl-ag.de
Make an appointment Enquiries by e-mail